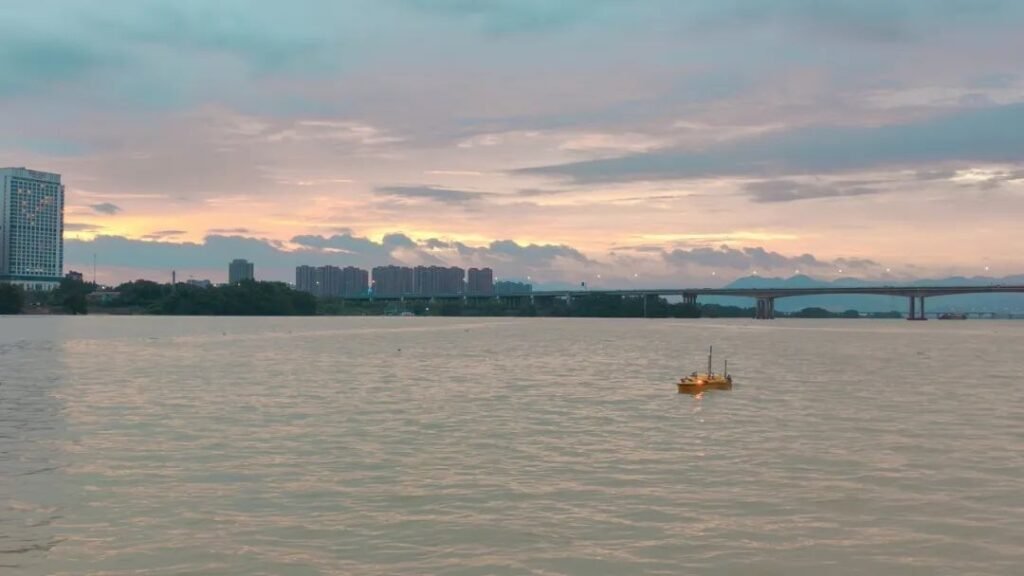
A bridge is an overhead structure with load-bearing capacity. As an important part of road infrastructure, it is of great significance for facilitating transportation and strengthening connections. However, a bridge is not built once and for all. In the subsequent period, it will be affected by complex terrain, landforms, geology, meteorology, hydrology and other natural conditions. It is particularly important to do a good job in bridge pier safety monitoring and provide continuous data support for protecting the pier foundation and maintaining the stability of the bridge.
Project Overview
Jinshan Avenue in Minhou County, Fuzhou City is connected to the Juyuanzhou Bridge in the west, crosses the Wulong River to the west along Jianping Road to the Shangjie hub of Fuyin Expressway (G70), and enters Fuzhou City through Jinshan Avenue in the east. As an east-west fast passage in Fuzhou City, it has important economic and social value. In order to build a solid bridge safety line, this project will conduct riverbed scour scanning and measurement of the Juyuanzhou Bridge, establish a three-dimensional point cloud model of riverbed scour, and provide data support for bridge pier safety monitoring.
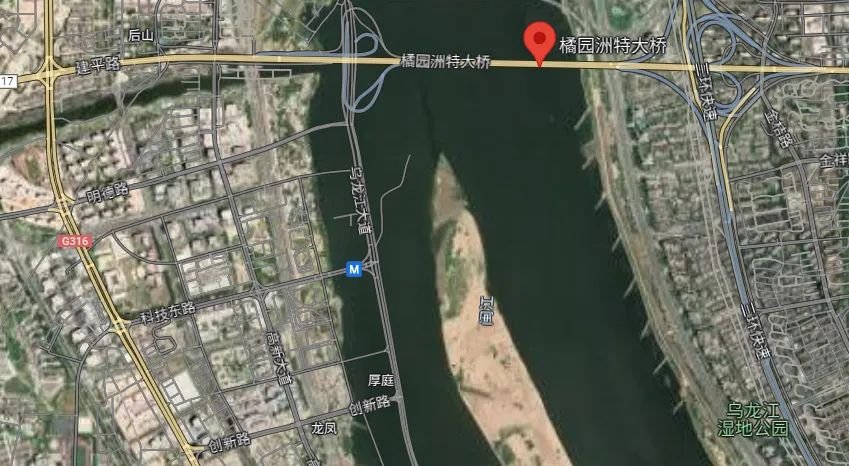
Traditional scanning dilemma
Although the method of using traditional artificial boats to carry multi-beam equipment to scan bridge piers has become increasingly mature, according to the actual situation in the survey area, this operation mode still has the following problems:
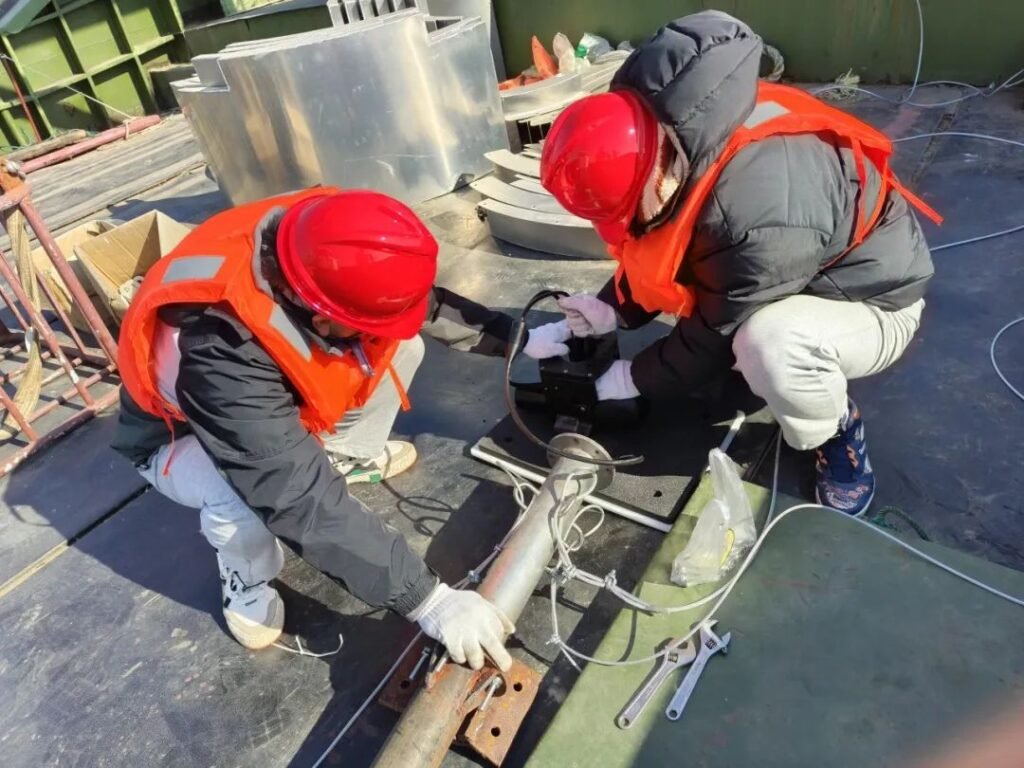
① Large safety hazards
On the one hand, due to the obvious changes in tidal water levels in the survey area, strong winds and waves, and ships passing through the waterway, the operating environment has a large risk factor; on the other hand, there are stone ridges on the banks of the river that can be submerged by high water levels. When using artificial boats to scan the riverbed, collision accidents are prone to occur near the bridge piers.
② Low operating efficiency
During the typhoon transit window period, the construction period is relatively tight, but the installation of multi-beam brackets and the calibration of ship equipment attitudes take a long time. In addition, in shallow water areas such as the edge of the river bank and near the sandbar in the middle of the river, a large number of underwater operations can only be carried out during a short period of flat tide, and the operating time requirements are strict, and the construction is extremely difficult.
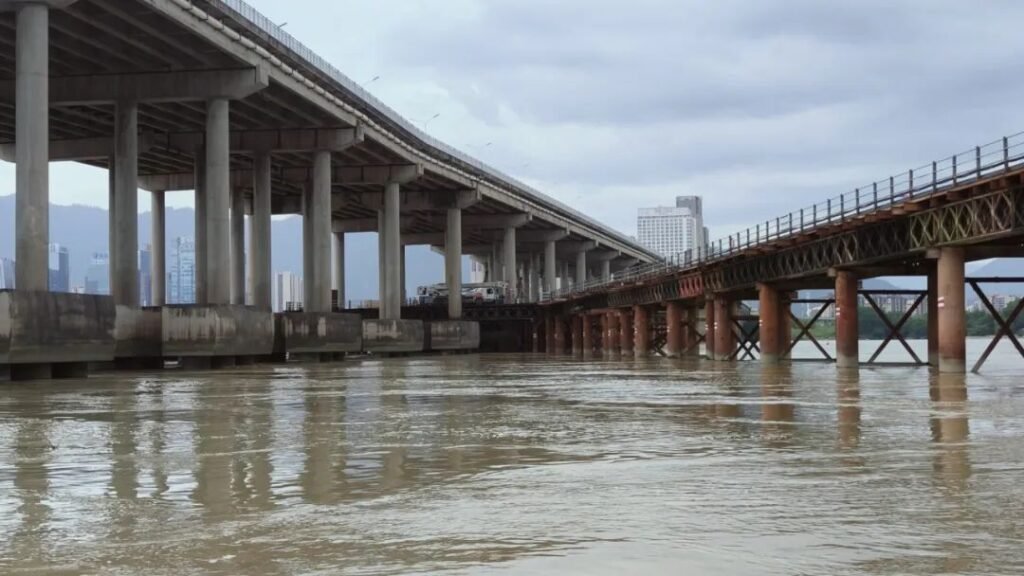
③ Poor data quality
During the multi-beam measurement process, the strip coverage rate is required to be above 20%. The accuracy of the artificial ship measurement line is often affected by the wind and wave environment and the driver’s experience. The overlap rate is insufficient or the probability of missed measurement is extremely high. In addition, the poor signal under the bridge will also affect the accuracy of satellite search, making it difficult to ensure measurement efficiency and data integrity.
④ High operating cost
There is a lack of ships and equipment suitable for underwater topographic mapping, and traditional artificial ships need to be rented, which results in high project costs.
The above mentioned the drawbacks of traditional scanning methods, is there an effective solution to these problems? Don’t worry, next, this article will focus on the riverbed scour scanning case of Juyuanzhou Bridge in the Minjiang River Basin, and introduce the riverbed scour 3D point cloud model: the practical application of HUACE No. 6 + NORBIT + iLiDAR integrated water and underwater measurement solution in bridge pier scour.
Efficient working method
HUACE No.6 is a large-space, multi-carrying, ultra-light all-carbon-body automatic unmanned boat platform. It is equipped with a NORBIT multi-beam bathymetric system as standard and an integrated iLiDAR 3D laser scanner to complete the integrated 3D point cloud data collection above and below the water. The system has the advantages of being highly integrated, lightweight, compact, easy to install, simple to operate, easy to carry, and low power consumption.
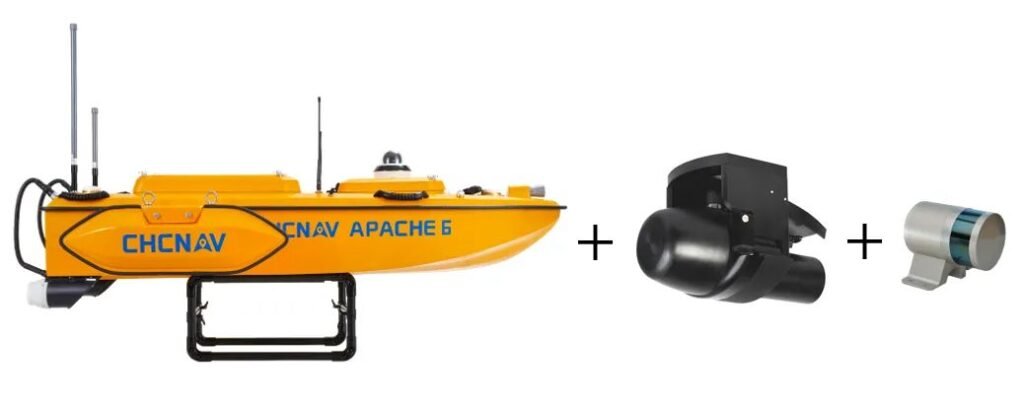
Huace 6+NORBIT+iLiDAR
【Huace 6】
Full carbon hull: The entire ship weighs 15kg, made of integrated carbon fiber, lightweight and sturdy;
Detachable in three parts: Suitable for both logistics transportation and nearshore wind and wave environments;
Straight-line route: Automatic cruise mode follows the planned route line;
Large capacity: Standard equipped with NORBIT multibeam, customizable to carry ADCP, water quality meters, side-scan sonar, and other equipment.
【NORBIT Multibeam】
210° opening angle: Doubles operational efficiency;
No installation calibration required: Integrated posture eliminates the need for complex slope calibration;
Time synchronization: Seamlessly stitches data above and below water surface;
Beam rotation: Can scan shallow areas and channel slopes;
Powered by lithium batteries: DC power supply for up to 10 hours without a gasoline generator needed;
Data sharing: Multibeam positions, headings, postures shared with iLiDAR to save costs.
【iLiDAR】
Super lightweight: Main unit weighs less than 3kg;
Highly integrated: Only one cable is needed to access all waterborne data seamlessly;
Shared with multibeam system:Time synchronization,data sharing;
Software compatibility:Compatible with mainstream multibeam data acquisition and post-processing software on the market.
Operation process
1、Installation and launching
Complete the equipment installation (this measurement uses Huawei No. 6 + NORBIT iWBMS multi-beam + iLiDAR laser radar), and select a suitable launching point.
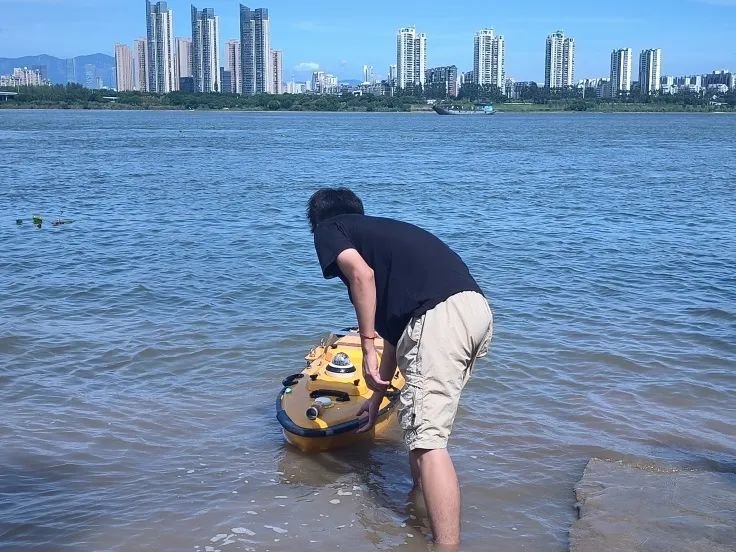
2、Attitude Correction
NORBIT multi-beam calibration without installation, fast “8” attitude calibration, real-time return of bathymetric data, remote monitoring of the measurement process.
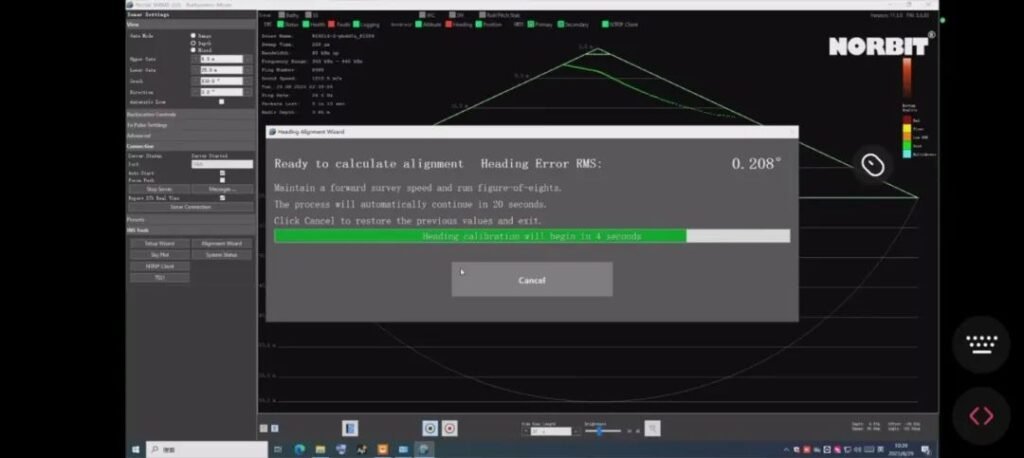
3、Data collection
① Use Autoplanner software to automatically plan the route for the unmanned ship, combine manual remote control to fill in the edge gaps, and use manual + automatic navigation to collect data.
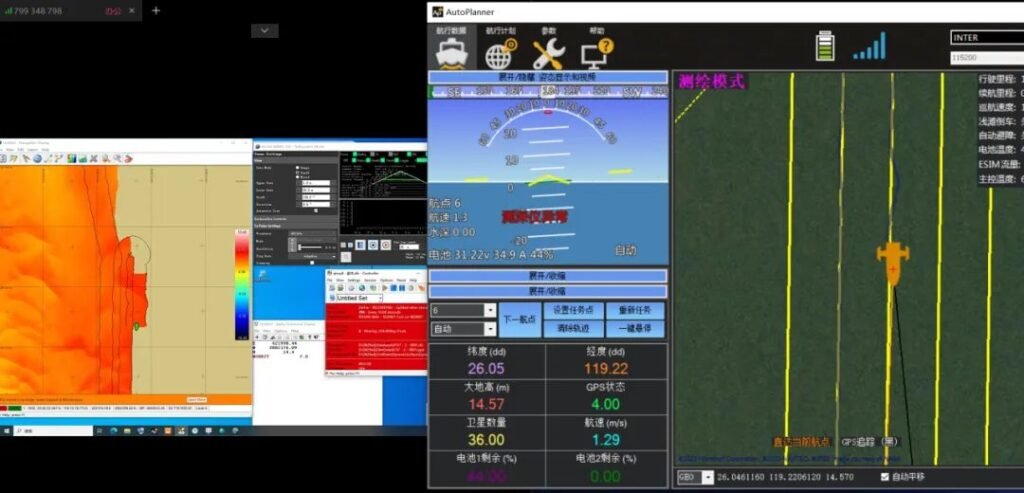
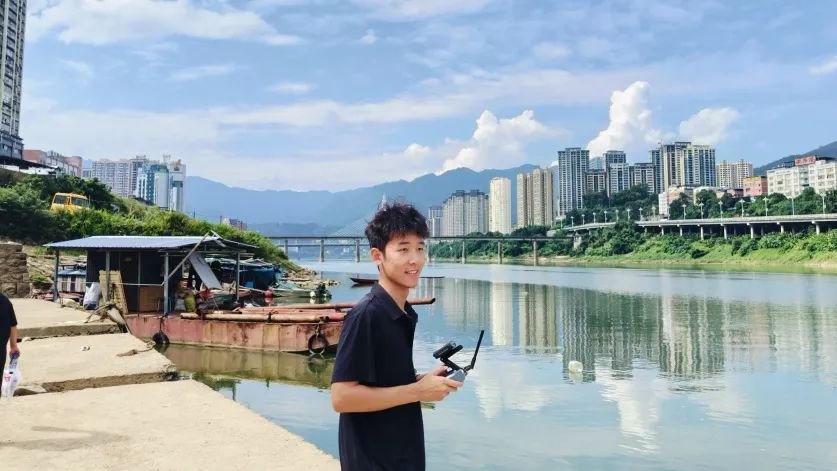
② Use QPS software to collect data on riverbed scour conditions, and ensure that the multi-beam strip coverage rate is above 20% during the measurement process.
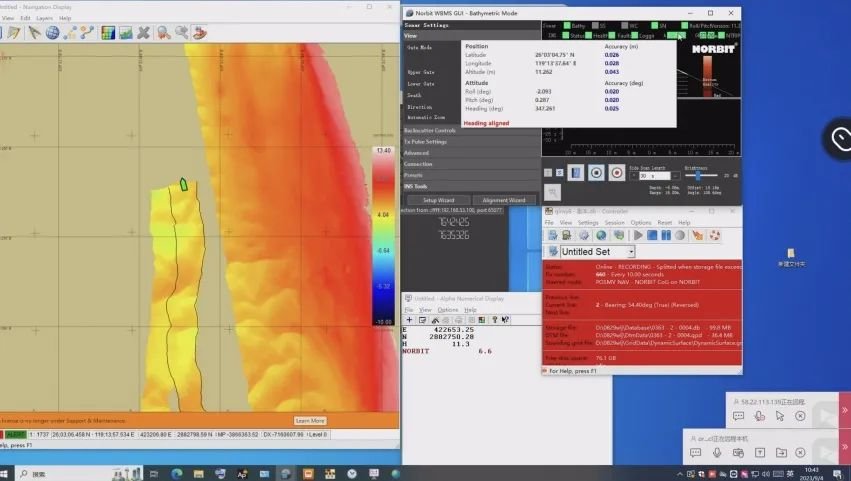
③Manually control the unmanned boat to sail back and forth along the Juyuanzhou Bridge and perform lidar scanning on the bridge piers.
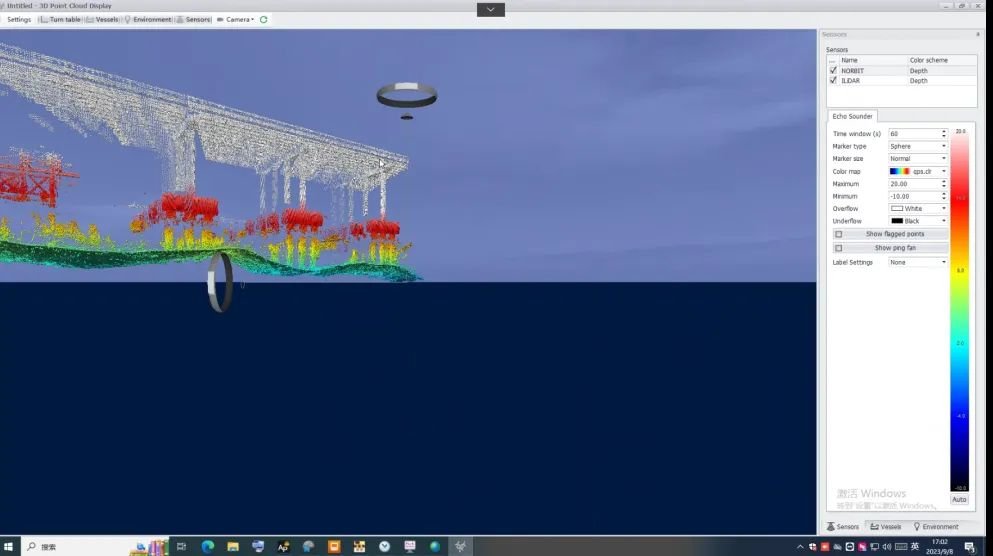
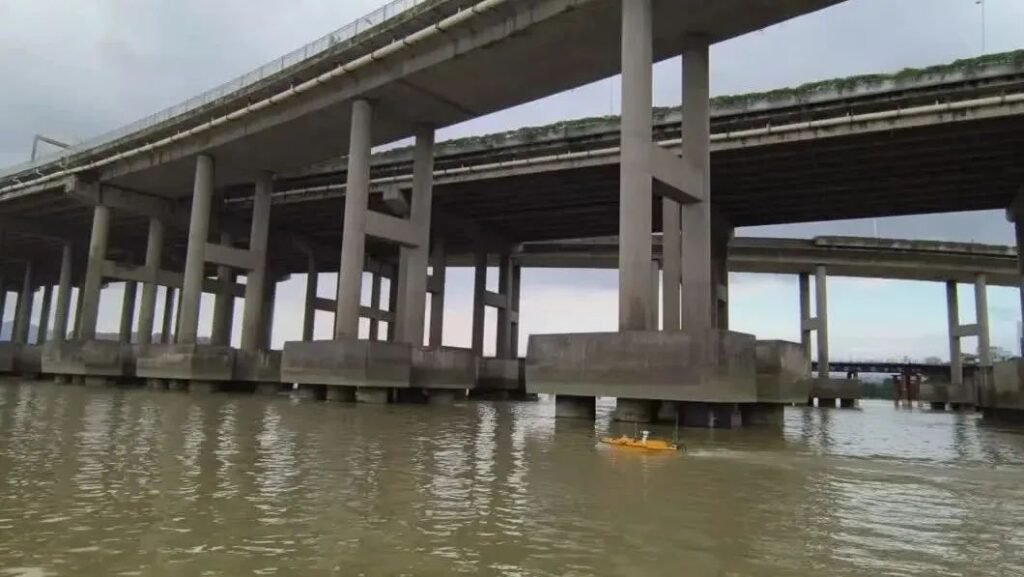
4、Data post-processing
Use QPS software for data post-processing to establish dynamic surfaces, with good data splicing quality and clear bridge pier scanning.
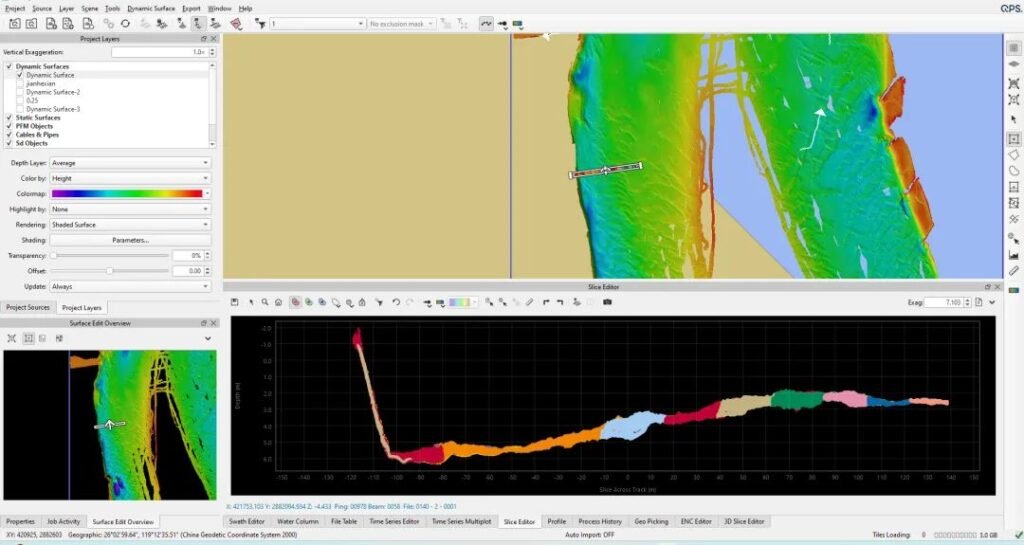
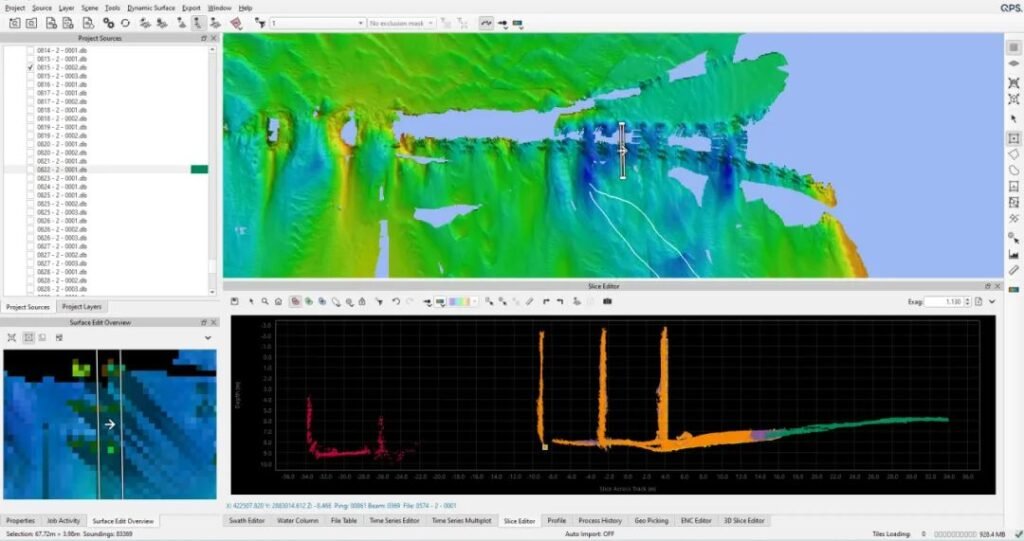
Achievements
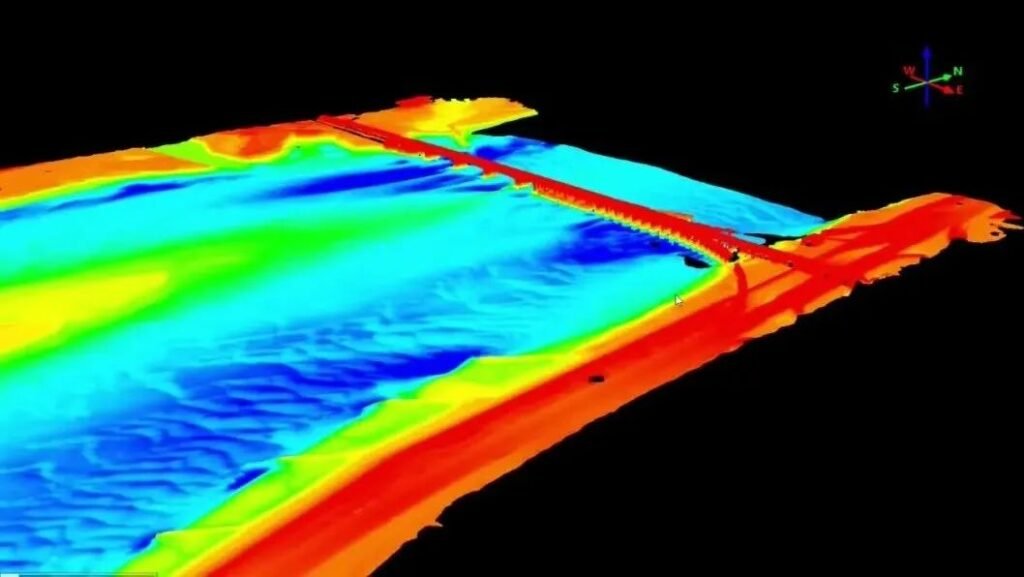
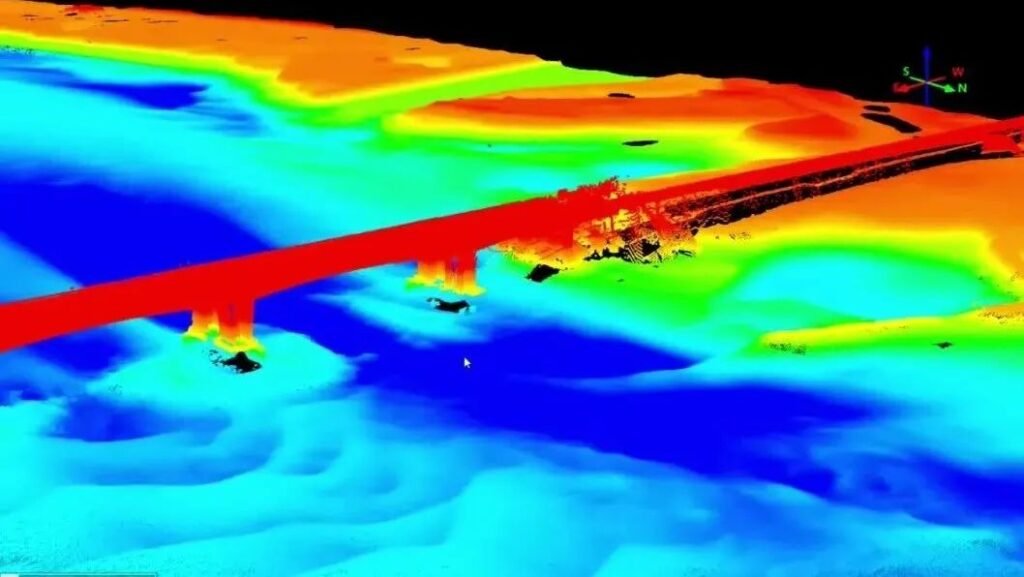
Summary
Compared with the traditional artificial vessels equipped with multi-beam equipment to scan bridge piers, the HUACE No. 6 + NORBIT + iLiDAR integrated water and underwater measurement solution has the advantages of high integration, light weight and compactness, safe unmanned operation, and low operating costs. It can not only ensure the safety of personnel and bridges, but also improve the operating efficiency exponentially while not fearing complex test environments such as bridge obstruction, ensuring collection efficiency and data integrity.
Application Areas
- Digital city construction (digital three-dimensional point cloud data collection of urban rivers and bridges, banks, greening, and buildings);
- Port applications (fine underwater measurement of ports and harbors, and detection of obstacles and shallow points, etc.);
- Energy applications (detailed measurement of offshore wind power pile foundation detection, offshore platform foundation morphology, and surrounding seabed scouring and silting conditions);
- Channel applications (digital channel underwater basic spatial data collection; navigation obstacle detection in safe waters; shipwreck scanning, etc.);
- Underwater engineering applications (precise calculation of earthwork volume for dredging, riprap, etc.; fine measurement of underwater buildings, etc.; fine measurement of residual materials after reef blasting, etc.);
- Marine oil applications (submarine pipeline laying, detection, and other related measurement work; detailed survey of submarine pipeline routes, etc).
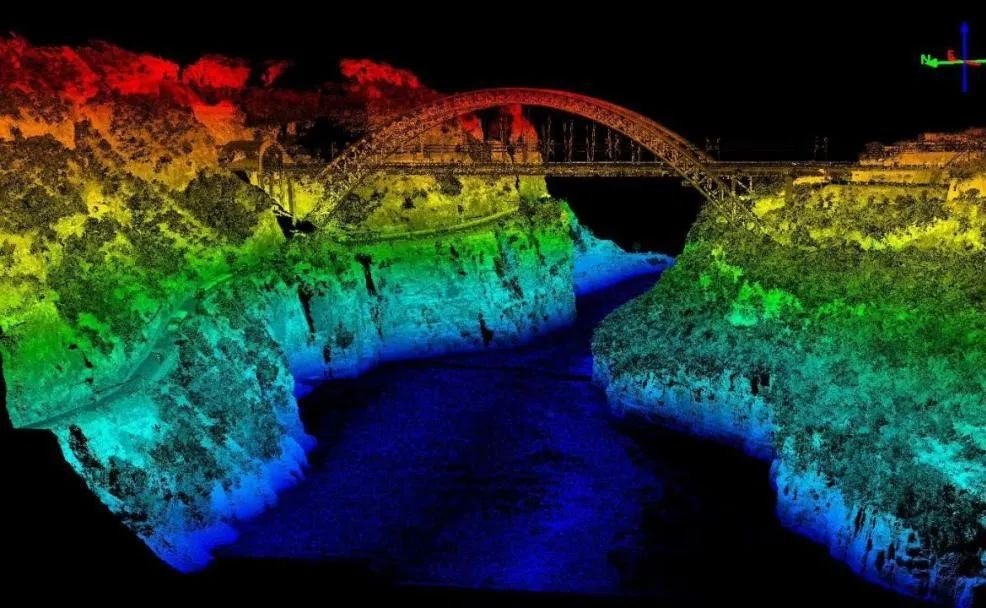
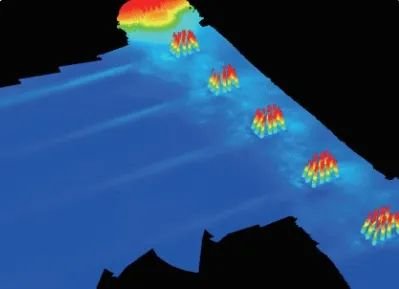
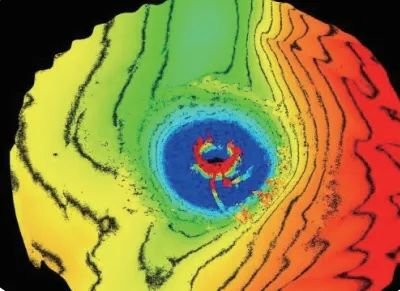
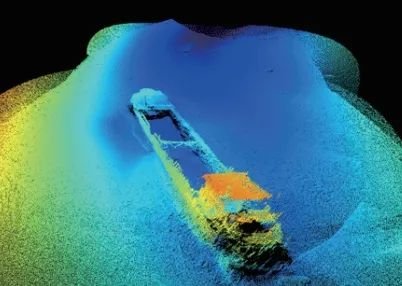
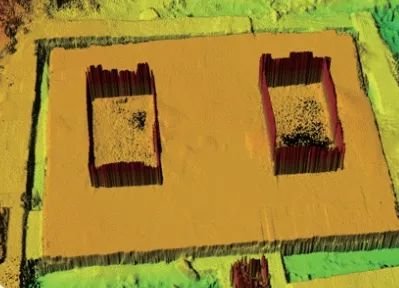
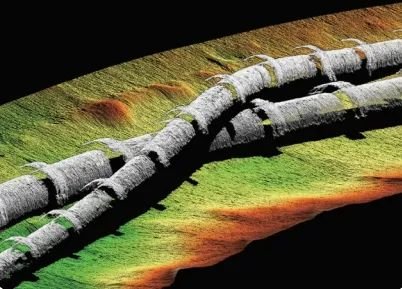